Fiber laser cutting is used in almost every modern industry due to the several benefits it provides.
Therefore, having an understanding of ‘what is fiber laser cutting’ and how it works may provide you with a new alternative technology for your particular industrial applications.
The good thing is that learning and using fiber laser technology is a lot simpler than alternative methods. This article will explore the in-depth working process of fibre laser cutting and its associated parameters. You will also learn about the various types of laser cutting operations, their benefits, limitations, and their different applications.
What is Fiber Laser Cutting?
Fiber laser cutting is a type of industrial laser cutting technology that uses the heat of a fiber laser for melting and removing the workpiece material, causing a clean cut. Laser stands for Light Amplification by Stimulated Emission of Radiation.
Fiber laser technology uses a very narrow light beam on the target material. The light is focused by a moving system of optics in the laser machine.
There are many different types of laser generation methods. Fiber lasers are named so because they use an optical fiber as the active gain medium for light amplification.
The optical fiber medium is doped with rare earth elements such as neodymium, ytterbium, thulium, erbium, etc.
When was Fiber Laser Cutting Invented?
The fiber laser was invented in 1961 by Elias Snitzer. He demonstrated this laser later in 1964. The evolution of lasers for cutting applications occurred in 1965 by Western Electric Engineering Research Center. These laser cutting machines were used to drill holes in diamonds.
The British further evolved the process in 1967 into laser-assisted oxygen jet cutting. Within a decade, laser cutting machines became common for cutting even the hardest materials, such as titanium, in aerospace applications.
What are the Main Components of a Fiber Laser Cutting System?
The main parts of a fiber laser cutting machine are:
Fiber Laser Source
Fiber lasers use a fiber doped fiber optic cable as the laser source. There are many different types of rare earth materials available for doping. This leads to multiple options for fiber laser source. Ytterbium-doped fiber lasers are among the most common types of laser source among fiber lasers. Different doping materials produce laser of different wavelength.
Cutting Head
The cutting head is the part that outputs the laser from the system and focuses it on the workpiece. It c a focus consists of a lens, a nozzle, and a focus tracking system. This is a movable part of the fiber laser cutting machine. The movement is according to the direction of the cut. The height of the cutting head from the workpiece is also adjustable.
Servo Motor
Servo motor is the part responsible for the movement of the optics and mechanical parts of the laser cutting machine. Modern laser cutting machines have precise servo motors capable of minute movements of the optical components. The speed of the servo motor is also highly controlled. The precision of the laser cutting is largely dependent on the movement of the servo motor.
Cooling System
Laser machine parts generate a high amount of heat. Therefore, it requires a cooling system to ensure the internal components are not damaged. This job is done by the water chillers. Water chillers can drop the temperature of the entire fiber laser cutter very quickly.
Worktable
The worktable is the area for mounting the workpiece. The worktable, bed, and beam are collectively called the host. The host contains various servomotors for the relative movement in the z-axis.
CNC Controller
One of the benefits of a fiber laser cutting machine is its ability to be automated through a CNC control system. The CNC controller interprets the program instructions and passes it along to the various parts of the machine. The CNC controller moves the cutting head in the X, Y, and Z axis accordingly.
Assist Gas System
The assist gas system is used to blow away the molten material from the workpiece. The laser beam is only capable of melting the workpiece material. Without the assist gas system, the molten material will cool-off and welding will take place. The assist gas system puts pressure on the molten material and pushes it away. The gas used may be oxygen, nitrogen, or air.
Control Panel
Control panel is the interface where the operator can interact with the machine and adjust various settings. The control panel also has features like the emergency stop button. There is generally a display to preview the settings and learn about any error codes and messages.
How Does Laser Cutting Work?
Here is a step by step breakdown of the working process of laser cutting systems:
1. Laser Generation
The laser cutting process starts with the generation of the laser beam. There is a separate laser generation system for this purpose. Laser generation is a multi-stage process that starts with the creation of light in the laser diodes. This initial light is also known as the pump light.
2. Guiding Pump Light Into Fiber Optic Cable
Fiber optic cable systems transfer the pump light beam to other parts of the machine. The fiber optic system consists of a fiber core and a cladding. The cladding is wrapped around the core and acts as a type of mirror for the total internal reflection of the laser beam. An optics cable also ensures that no light beams escape the core, leading to complete efficiency.
3. Light Amplification
Light amplification occurs in a special chamber of the fiber optic cable. This chamber is doped with rare earth materials like Ytterbium. When the light rays interact with the doped particles, the electrons of the particles get excited to a higher energy state. When these electrons fall back to their native state, they release energy in the form of light. Continuous excitation and relaxation of the photons create a light of high intensity. This is how an amplified laser beam is produced. A system of mirrors in the laser cavity are used to guide this light in the right direction.
This is also where the differences in the wavelength of different materials come into effect. Different materials have different excitation and relaxation states of the electrons. Therefore, they release different types of photons. This results in material-specific wavelength characteristics of the laser beam.
4. Laser Focusing
The laser travels to the cutting head through a series of internal optical system. The laser cutting system can move around the workpiece. Therefore, the optical system aims to ensure the required laser focus and diameter remains unchanged. Some laser cutting machines skip on the internal optics and instead add the ability to move the workpiece around a stationary cutting head. The laser is output from the machine through the cutting head. The cutting head contains a high-quality lens to focus the laser beam to a very narrow width.
5. Material Interaction
The laser beam falls on the material at the required spot. The energy from the laser beam is transferred to the material particles. This heats the particles and melts them instantly. The laser works in tandem with the gas assist system that blows the molten material as soon as the laser melts it. This results in the characteristic clean cut of the fiber laser cutting process.
Various Parameters of the Fiber Laser Cutting Technology
Working with fiber laser technology requires understanding the several parameters associated with the process. These parameters are:
- Laser Modes: Fiber laser cutting can operate in two modes- continuous wave (CW) or pulsed wave (PW). The pulsed mode has very short pulses of laser beam separated by short pauses.
- Laser Power: Laser power is the average energy stored in the laser pulses. High power fiber lasers will be able to cut more challenging materials. The laser power is measured in Watts (W). The required laser power depends on the type of material you will cut with the fiber laser cutter. An important thing to note is that laser power is the average output power. A continuous laser of 100W power will emit 100W pulses. However, a pulse laser of 100W power can emit pulses as high as 10,000W.
- Pulse Frequency: Pulse frequency means the number of pulses per second. It is measured in Hertz (Hz). A higher pulse frequency transfers more heat to the workpiece particles resulting in faster cutting speeds and smoother edges.
- Beam Diameter: Beam diameter is the thickness of the laser beam. A lower beam diameter is preferred for a minimal kerf width and a highly precise cutting operation.
- Gas Pressure: Gas pressure is the parameter associated with the assist gas system. It details the pressure (flow rate in some cases) of the gases used to blow away the molten materials.
- Cutting Speed: The cutting speed refers to the linear length of the material that the fiber laser cutter can cut per unit time. It is expressed in inches per minute (IPM) or millimeters per minute (mm/min). Generally, thin materials or high power fiber lasers lead to a higher cutting speed.
- Material Thickness: The material’s thickness influences the cutting speed and the laser power you require. It can also influence the cutting quality. A higher thickness will reduce the cut quality when it comes to laser cutting.
- Lens Condition: Lens condition refers to the status of the focal lenses in the cutting head. The lens should be in good condition and free of any smudges or dirt. Damaged or dirty lenses will produce a low-quality cut or have a reduced cutting performance.
- Focal Point: The focal point of the fiber laser has the highest concentration of energy. The workpiece is kept at the focal point. The focal point is then adjusted according to the material thickness and the cut depth.
- Type of Material: Different materials have different physical characteristics. Laser cutting performance depends on factors such as material reflectivity and thermal conductivity.
- Preheating Material: The laser can take too long to melt and cut the workpiece for some materials. In such cases, the workpiece requires preheating before cutting with fiber lasers.
- Cutting Path: A linear cutting path is fast and easy to cut. However, complex paths reduce the cutting speed and require higher control over the fiber lasers. The laser cutting will be slowest at sharp corners.
What are the Different Types of Fiber Lasers?
There are many different classification systems for fiber lasers. These are:
Based on Laser Source
Fiber lasers are classified according to the doped materials. Some of these fiber lasers are:
- Ytterbium-doped Fiber Lasers: Ytterbium-doped lasers have a wavelength of 1064 nm. These fiber lasers carry high power and high efficiency. In addition to cutting, they are also used for laser marking, engraving, and welding.
- Erbium-doped Fiber Lasers: Erbium-doped fiber lasers have a variable wavelength. The two most common wavelengths are 980 nm and 1480 nm. This wavelength provides the ability for long distance travel. Therefore, erbium-doped fiber lasers find applications in the medical sector, telecommunications, and spectroscopy.
- Thulium-doped Fiber Lasers: Thulium-doped fiber laser has a variable wavelength between 1810 nm to 2100 nm. Thulium-doped fiber lasers are common in sensors and medical applications.
Based on Operating Mode
Laser cutting machines have multiple modes of operation, such as:
- Continuous Wave Laser: Continous wave laser outputs one single laser beam continuously throughout the cycle. Continous wave laser is good for both laser cutting and laser welding. The rated power is the actual laser output power in this mode.
- Pulsed Wave Laser: Pulsed wave laser emits short durations of laser pulses. The output power of each pulse is considerably higher than the rated laser power. There are many different types of pulsed wave fiber laser modes, such as q-switched and gain-switched.
Far-field Distribution
There are two models of fiber laser cutting based on the far-field distribution characteristics of the laser beam:
- Single-Mode Laser: A single-mode laser has a single peak with a bell shape. The width of these lasers is low, leading to a low contact area and low power transfer.
- Multi-Mode Laser: Multi-mode fiber laser has multiple peaks and a large core diameter. The higher core diameter means these lasers can transfer a higher power to the workpiece material.
What Materials Can a Fiber Laser Cut?
A fiber laser cutting machine can work on a wide range of materials, such as:
Metals and Alloys
Lasers can cut any metals and metal alloys. This includes ferrous and non-ferrous materials. Some examples of metals and alloys that fiber lasers cut are:
- Aluminum
- Copper
- Steel
- Stainless Steel
- Titanium
- Brass
- Carbon Steel
Wood
A fiber laser can cut through wood without generating any sawdust. The process applies to all types of woods. However, appropriate fire prevention safeguards should be used when cutting wood with a laser cutter. In addition, ensure that the wood does not contain any flammable paints or oils. Some common woods cut by fiber laser cutting machine are:
- Hardwood
- Softwood
- Laminated wood such as MDF
Paper and Paper Products
Lasers can create intricate cuts on paper and products such as cardboard. These capabilities are used in decorative cards and wedding invites.
Plastics and Composites
Plastic cutting is a sensitive area for lasers. It is important to ensure that the fumes generated by the plastic do not cause damage to the fiber laser optics. Therefore, you can cut with a laser with limited choices of plastics and composites. However, fiber laser can cut hard composites like carbon with ease.
Miscellaneous
Besides the above materials, there are also many more that can be cut with a fiber laser. These are:
- Diamond
- Ceramics
- Tungsten
- Graphite
- Silicon
Benefits of Fiber Laser Cutting
Fiber laser cutting provides several advantages when compared with alternative industrial cutting technologies. Some of these are:
- No Material Dust: The material removed by the laser cutting machine is melted and removed away. Therefore, there is no generation of dust. This creates a clean workspace.
- No Cutting Tool: A fiber laser does not have a physical cutting tool and is not friction-based. Therefore, you don’t have to deal with frequent tool wear and replacements.
- High Precision: The accuracy of the laser cutting process is second to none. It is the most precise cutting technology due to the extremely thin profile of the laser light.
- Versatility: A fiber laser system can cut any material, whether a conductor or insulator. Therefore, it is highly versatile without requiring different tooling or equipment for different materials.
- Automation: Fiber laser machines can be integrated with automated systems such as Computer Numerical Control (CNC). This means the programs can control the machine’s movements without manual intervention.
- Energy Efficiency: The energy requirements of a fiber laser machine are considerably lower than other cutting machines. This makes it a very energy-efficient cutting solution.
- Speed: A fiber laser cutting machine can cut material at a speed as fast as 3 meters per minute. This leads to high productivity.
- Operating costs: A fiber laser cutting machine has no tooling requirements and minimal running costs. This keeps the operating costs to a minimum.
Limitations of Laser Cutting
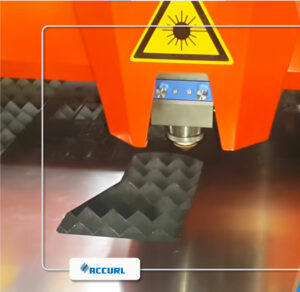
Laser cutting has a high versatility and is a widely adopted technology. Even so, there can be certain limitations to a fiber laser cutting machine for some users. These limitations are:
- Material Limitations: Certain materials such as plastics emitting toxic gases cannot be cut with a fiber laser cutting machine. These materials include PVC, ABS, Polycarbonate, and HDPE.
- Maintenance and Service: A fiber laser cutting machine requires proper maintenance and periodic service. Ignoring the maintenance can lead to damage to the internal parts such as the focus lenses. This can reduce the cutting performance significantly.
- Initial Cost: While the operating costs of a fiber laser cutting machine is low, there is still some initial investment required to purchase the equipment. The only consumable for these lasers is electricity.
- Material Thickness: A fiber laser can only cut materials up to a certain thickness of around a few centimeters. This may be less than what is required for certain applications.
How to Choose a Fiber Laser Cutting Machine?
When choosing a fiber laser cutter, evaluate your options based on the following parameters:
- Material Type: Decide the type and thickness of the material you will be cutting. This will narrow down the range of available options.
- Cutting Speed: Different machines have different operation speeds. Choose a machine with enough speed to meet your production requirements.
- Automation: If you want an automated system, choose a machine that supports a control system, such as the CNC.
- Safety Standards: The safety standards of the machine are important for the safety of the operator and the workspace.
- Brand: The brand value is important for heavy equipment such as a laser solution. It consists of sensitive parts like optics lenses. Therefore, any quality issues can cause frequent breakdowns and long downtimes.
Applications of Fiber Laser Cutting Machine
A fiber laser cutter is used in a wide range of industries, including:
- Automotive
- Metal Fabrication
- Aerospace
- Electronics
- Decorations
- Printing
- Kitchenware
- Lighting
- Manufacturing
- Advertising
- Aerospace
Are there any challenges of fiber laser cutting?
The main challenge of fiber laser cutting is the thickness of material that can be cut. Laser cutting technologies are good for material sheets but don’t work well for thick blocks.
In addition, cutting toxic materials emit gases that settle in the optics and damage them irreversibly.
What maintenance is required for a fiber laser cutting system?
The major maintenance requirement of the laser cutting system is to ensure the cooling system is doing its job. This includes period checks on the filters and level of coolants.
The lens and mirrors also require cleaning to remove any settled dust. A clean fiber optics system will provide a better beam quality.
Are there any environmental considerations or regulations associated with fiber laser cutting?
The main environmental consideration with using fiber laser solution for cutting is the generation of smoke, gases, and aerosols. It is important to check with local rules to know if there are any regulations in the disposal of such waste.
How long does a fiber laser system last?
A fiber laser system can last for over 50 years with proper use and maintenance. This equates to about 100,000 working hours for the machine.
In comparison, CO2 laser cutting machines have a lifespan of only around 10 years.
How much does a fiber laser cutter cost?
The cost of a fiber laser cutter can vary between $30,000 to $500,000. The wide price bracket is due to variances in parameters such as machine features, degree of automation, laser power, etc.
Focusing on the machine quality can provide better results and return on investment instead of sorting products based on the initial cost.
Accurl’s fiber laser cutting machines provide the best value for money in this regard. These machines combine a high-quality IPG fiber laser source with a rugged construction. The machine has features such as graphite anti-burn technology to protect every part of the bed and worktable from laser burn. There are many products to choose from in the catalog to suit particular requirements and budgets.
What is the difference between fiber laser technology and CO2 laser?
The difference between fiber laser and CO2 laser is the type of laser system. Fiber laser uses a rare earth material doped fiber optics laser cavity to generate the amplified light beam.
On the other hand, CO2 laser uses a gas discharge tube to produce laser light.
Conclusion
A fiber laser cutting machine is a great way to cut any material without any operating costs involved with tooling or cutters.
Modern fiber laser cutters can cut metals with the hardest machinability. This makes laser cutting solutions an excellent investment for all industrial applications.
If you want to add a laser cutter to your workshop or manufacturing facility, get in touch with Accurl to know the best fit for your requirement.
Frequently Asked Questions
Here are the answers to some common questions regarding laser cutting machines:
1. What is the frequency of fiber laser cutting?
The frequency range of fiber laser cutting can vary between 20 KHz to 200 KHz. The useful frequency bracket is quite lower, generally around 50 KHz to 100 KHz. This frequency range depends on the power of the laser being used.
2. How thick can a 1 kW fiber laser cut?
A 1 kW fiber laser can cut material as thick as 20 mm. The maximum thickness depends on the type of material being cut. For instance, while a 1 kW laser can cut 20 mm carbon steel, the maximum thickness for stainless steel is only 10 mm.